2、主要生产工装设备名称、数量
我公司设有铸造,加工,装配等3个车间。目前高铬铸铁年生产能力10000吨,单件最大生产能力20吨。铸造车间拥有先进的连续混砂机,铸件全部使用树脂砂造型,炉前成分检验采用直读光谱分析仪,结合先进的耐磨合金冶炼技术,铸造工艺和热处理工艺,保证铸件表面光洁,内部组织致密和质量可靠。公司工艺先进、手段齐全,拥有主要生产设备近50台。

部分设备列表如下:
检验设备 |
编号 Item | 设备名称 | 型号 Type | 数量 Qty. |
1 | 分析天平 | TG328A(s) | 1 |
2 | 可见分光光度计 | 722N | 1 |
3 | 液压式万能强度试验机 | SWY | 1 |
4 | 箱式电阻炉 | 4-13 | 1 |
5 | 电弧燃烧炉 | OFK-1A | 1 |
6 | 碳硫联测分析仪 |
| 1 |
7 | 水分测定仪 | KF-1 | 1 |
8 | 旋转粘度计 | NDJ-1 | 1 |
9 | 微机屏显液压万能试验机 | WEW-300D | 1 |
10 | 电磁微震筛砂机 | SSD-A | 1 |
11 | 摆锤式冲击试验机 | JB-300B | 1 |
12 | 制度光谱仪 | GS1000 | 1 |
我公司有完善的计算机设计、生产及管理系统。在计算机网络和数据库支持下的实现企业产品设计、开发,企业生产经营管理以及质量控制系统全部实现微机化。整个系统分为CAD/CAM计算机辅助设计制造系统;CFD计算流体动力学分析系统;CAE计算机模拟铸造分析系统;计算机辅助工艺设计CAPP和工艺数据管理软件系统。
3、主要试验设备名称、数量、容量、可试验项目
我公司内与浙江大学合作建成有测试精度达到国际先进水平的大型高压及低压试泵站,该试泵站利用微机实现对各种泵试验全过程的自动控制、自动采样和试验数据的计算处理。亦可通过人工/自动切换开关转换到手动状态, 由人工操作控制试验过程。
我公司的试泵站由高压试验区和低压试验区,占地面地为432平方米,试验水池容积1000立方米,深度7米,可测试流量范围0-12000m3/h、扬程0-1.6Mpa,起重能力32吨。高压试验台试验能力:工作功率最大为1600kw,电压为6kv/10kv,最大流量12000m3/h,扬程为100米;低压试验台分有低压水卧式水泵试验台2个和低压立式潜水试验台1个,工作功率为315kw(低压卧式泵试验台)/200kw(立式潜水泵试验台),最多流量4600m3/h。扬程160米。试验项目: 315KW以内配套电动机的空载试验、150KW以内配套电机的负载试验及电机绕组直流电阻的测定(电测功方法时使用),并出具电机试验报告;泵的性能试验(电测功或扭矩测功) ;泵的汽蚀试验(电测功或扭矩测功);噪声试验;振动试验。
试验泵站控制室

试验泵站全景
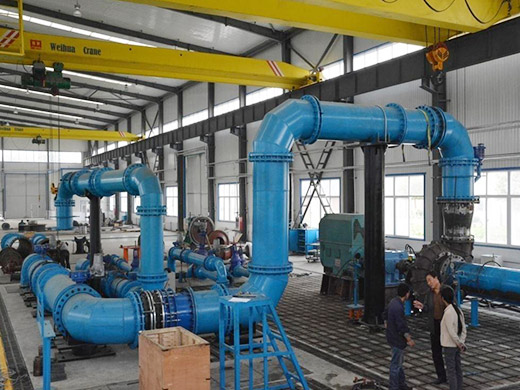
完善的检测设备和一流的试验、检验人员为设备的质量提供了强有力的保障。 部分检测设备列表如下:
编号 | 设备名称 | 数量 |
1 | 分析天平 | 1 |
2 | 可见分光光度计 | 1 |
3 | 液压式万能强度试验机 | 1 |
4 | 水分测定仪 | 1 |
5 | 旋转粘度计 | 1 |
6 | 微机屏显液压万能试验机 | 1 |
7 | 摆锤式冲击试验机 | 1 |
8 | 制度光谱仪 | 1 |
4、公司设计能力
现有各专业高中级设计人员30余人。研究所和技术中心科研手段齐全,拥有供科研人员研究试验使用的现代化试验平台,包括ISO3555B级精度的半自动清水性能试验台、渣浆性能试验台、快速寿命试验台、流量计校验装置以及回转转盘磨损试验机、金属耐磨材料试验装置等先进的试验研究设备和测试装置,专门从事杂质泵设计理论、水泵性能、磨损机理、耐磨材料、新工艺和新产品开发的研究工作。
目前,公司的产品开发、设计和工艺设计等在全国泵行业率先采用计算机辅助技术,并全部实现联网和信息共享,建立了完备的CAD硬件平台和软件平台,拥有SUN工作站,拥有微机150余台。采用I-DEAS的工作平台,实现了产品零件的三维建模、表面设计、装备干涉检验及有限元分析,还可以利用计算机做壳体的强度分析和轴隙的模态分析,从而使产品设计—工艺设计—新产品计划管理—科研计划管理—图纸和有关资料提供全部电子化。
5、采用的新技术和改进项目
(1)计算机辅助铸造技术
铸造件在水泵零件中占有的比例较大,很多关键零件均铸造生产,我公司对铸造过程有严格的控制规程与先进的控制手段。
我公司引进先进的连续混砂机,并采用树脂砂造型,结合先进的耐磨合金冶炼技术,保证了壳体的铸造水平及过流面的光滑水平。为保证铸件材质,我公司花费200多欧购进德国光电直读光谱仪用来进行炉前材质控制:当液态金属出炉时,取样、化验各种金属成分是否合格及液态金属的流动性,保证部件的金相组织均匀、致密,出厂设备无铸造缺陷,使生产用户运行中的设备不会因为过流部件铸造缺陷造成寿命短而停产造成经济损失,同时,也保证了我公司对用户的承诺落到实处。
近年来,我公司又引进了先进的计算机铸造工艺分析系统(CAE/InteCAST)。华铸CAE能够模拟分析铸造过程中的流动问题、传热问题以及二者的耦合计算。流动与传热耦合计算能够得到流动过程的温度分布,从而保证了铸造流动过程及后续凝固过程模拟计算的准确性。针对不同铸造方式,不同合金种类,采用合理的处理手段,InteCAST 能够快速准确地对各种铸件的凝固过程进行模拟分析。利用流动及传热分析技术,CAE能够对铸造浇注系统进行分析,评判浇注系统性能的优劣,提出改进措施,达到优化浇注系统的目的;同时还能够对金属模具进行分析,优化模具壁厚,确定模具预热温度,判断模具热疲劳程度,给出模具冷却工艺等,达到优化模具设计,提高产品质量的目的。
基于当代最新流体力学技术,CAE采用先进的数值求解方法,能够在计算机上实现对复杂真实铸件流动充型过程进行模拟分析并模拟铸造生产的充型、凝固过程,预测可能产生的缩孔、卷气、卷渣等铸造缺陷,提出改进工艺的有效措施,降低废品率,保证铸件的质量不存在缺陷。
(2)CFD技术
我公司渣浆泵的水力设计在国内处于领先地位,我们采用CFD(computational fluid dynamics计算流体动力学)技术,利用CFD软件对水泵内部流道流场和外部特性进行预测,模拟浆体在泵腔内的运动,合理调整叶片包角和叶片厚度,使其具有较宽的过流通道,降低流道内的相对流速,从而减少输送浆体对过流部件的冲击,降低过流件的磨损率,提高泵的水力效率。这些新技术的应用表明我公司在产品的设计开发与制造方面,已经达到国内先进水平。